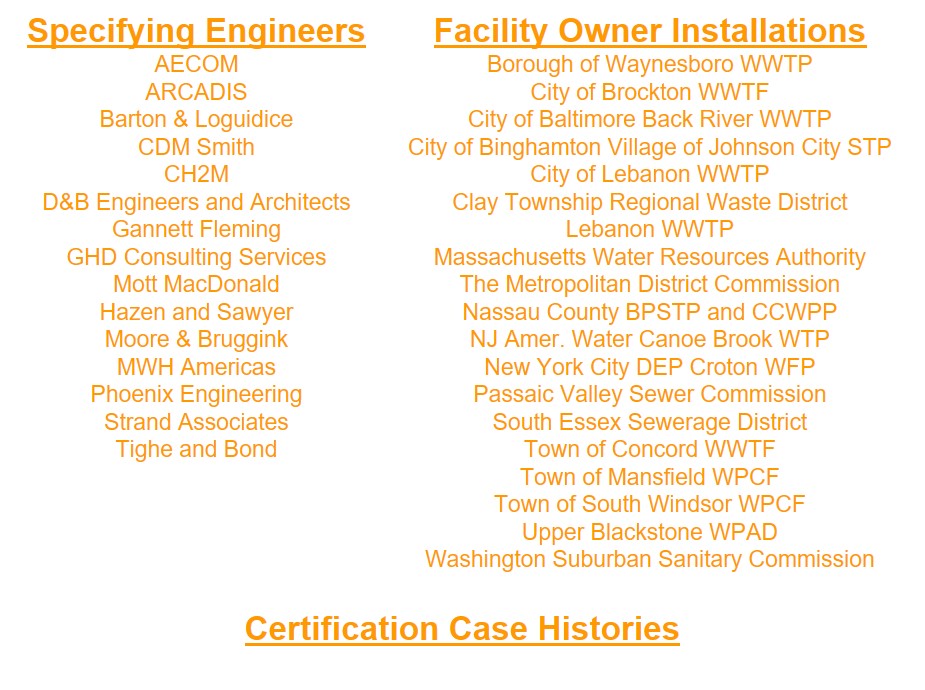
|
Gannett and Fleming Specifies FRPI Certified Tanks Borough of Waynesboro Wastewater Treatment Plant is the home of one (1) 8’ ID 65% Magnesium Hydroxide mix tank plus two (2) 9’ ID 45% Aluminum Chloride storage tanks. Kinsley Construction installed them at this Waynesboro, PA, facility following specifications by Gannett and Fleming. The tanks were fabricated by Justin of Georgetown, DE. The 9’ Aluminum Chloride tanks included ladders and flat tops for ease of access, whereas the mix tank included an integral agitator bridge supported on the tank. City of Lebanon Upgrades 1962 Wastewater Treatment Plant. | 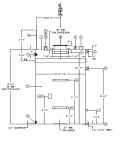 | | 9’ Ø Aluminum Chloride Tank |
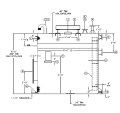 8’ Ø Magnesium Hydroxide Mix Tank | City of Lebanon Upgrades 1962 Wastewater Treatment Plant Justin Tanks provided two (2) 10’ ID 41% Ferric Chloride storage tanks with ladder access to flat tops for ease of access plus two (2) 8’ ID 65% Magnesium Hydroxide mix tanks with mixers and platform supported by tanks. Gannett and Fleming specified FRPI Certified tanks for this upgrade, which were installed by Allan M. Myers at the Lebanon, PA, facility. The tanks are included in a chemical treatment process utilized to reduce the amount of nitrogen discharged into the Chesapeake Bay Watershed, protecting the Waters of the Chesapeake Drainage area.
|
| |
FRPI Certified Tanks at New Jersey Award Winning Facility CDM Constructors installed two (2) 8’-6” ID Sodium Hypochlorite tanks at the award winning New Jersey American Water Canoe Brook Water Treatment Plant in Short Hill, NJ. The Tanks were specified by CDM Smith and manufactured by Justin Tanks for this new state-of-the art facility that will provide New Jersey residents up to15 million gallons of drinking water per day. Postcure for tanks was performed by Justin following FRPI SB02 practices in order to assure maximum chemical resistance of DMA/BPO cure system utilized for the tank’s inner corrosion allowance plus meet FDA requirements for fiberglass used in drinking water applications. | 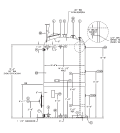 8’-6”’ Ø Sodium Hypochlorite Tank
|
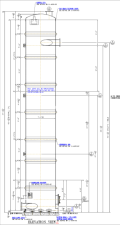 7’ Ø Stock Retention Tower | Paper Industry Installs 1st FRPI Certified Tower A prominent pulp producer in Southeastern United States received forty (40) years of maintenance free service from their 7’ ID FRP Chlorine Dioxide Stock Retention Tower and wanted to assure similar performance with its replacement on a competitive level playing field for prequalified manufacturers. So they engaged Corrosion Probe to write the specification for Tower purchase, which included a design basis with lessons learned from this bleached pulp stock application and FRPI Certification. The Tower was manufactured by An-Cor in North Tonawanda, NY, shipped across the country and successfully installed by an onsite rigger to meet the mill startup schedule following a 250’ blind lift to get it into position.
|
SESD Utilizes FRPI Certification for Second Time | The South Essex Sewerage District of Salem, MA was the first to require FRPI Certified odor control ductwork in 2006, which replaced a stainless steel system experiencing heavy Microbiologically Influenced Corrosion (MIC). They found success with the certification process and specified certification for their next fiberglass project involving replacement of four (4) 10’ ID 15% Sodium Hypochlorite thermoplastic tanks with fiberglass tanks. Tighe and Bond was the specifying Engineer, with Methuen Construction performing installation early in 2012. The tanks were manufactured by An-Cor and installed through removable building walls planned for ease of future replacement of the thermoplastic tanks provided with the original facility design in 1996. |
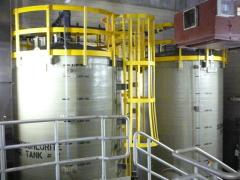 10’ Ø Sodium Hypochlorite Tanks
|
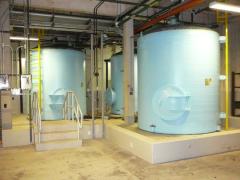 9’ Ø Aluminum Chloride Tank
| Second Round of FRPI Certified Tanks The Upper Blackstone Water Pollution Abatement District together with CDM Smith (formerly Camp, Dresser and McKee) were the first to specify FRPI Certified tanks in 2003, which were installed in 2004. Their Satisfaction with specification development, submittal review, manufacturing and installation support on the first round of tanks led to a preference for Certification on the second round installed by William M. Collins Company in 2011. Three (3) 9’ Ø Mannach Polymer tanks were manufactured for this Millbury, MA wastewater treatment operation by An-Cor.
|
Methuen Construction Supports FRPI Certification |
With experience on three (3) installation projects involving FRPI Certification and dozens of other fiberglass related work under their belt over the past five (5) years, Methuen has learned FRPI is making a difference and improving industry. A number of Project Managers at Methuen, like many contractors, have first hand involvement discovering fiberglass equipment shipped to their sites did not meet spec, had to be dealt with and cost the project more than expected. In a recent case one (1) 12’ diameter 10 PSIG carbon absorber catastrophically failed, resulting in all five (5) being pulled from service and re-built costing the system supplier hundreds of thousands in unplanned repair costs. Although a challenge at first, Methuen supports FRPI Certification and encourages Engineers and Owners to specify this method of Quality Verification for everyone’s benefit. | |
South Windsor WPCF in Connecticut Receives “beefy” Sludge Tank |
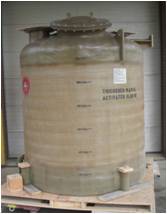 | The new South WIndsor WPCF tank was designed for municipal sludge having a specific gravity of 1.1, with potential sludge surcharge back up loading to 39’ elevation and imposing approximately 6 PSIG pressure on tank. CH Nickerson purchased this FRPI Certified tank from An-Cor DKG, which was manufactured in accordance with Camp Dresser and McKee specifications. A custom engineered hold down system and pressure vessel design following industry standard engineering rules was necessitated by the application. |
AECOM (formerly Metcalf & Eddy) Joint Venture with Hazen and Sawyer on New York City DEP Croton WTP Project |
Thirty-eight (38) tanks were shipped to the New York City DEP Croton Facility. The applications ranged from 15% Sodium Hypochlorite Bulk to UV Cleaning System Waste Storage. Design basis included 2’ depth of buoyancy force, 5 PSIG field hydro test after installation and Level 1 ASME RTP-1 allowable visual defects. FRPI SB01 Level I Engineered Post-Cure and SB03 Preparation for Food Grade Product Contact material treatments were also performed for long term laminate performance. To assure reliability of the flat bottom and top tanks, An-Cor DKG shop hydro tested and proved design in a restraint system built for the project. All tanks met or exceeded contract quality conformance specifications and were FRPI Laminate Certified. Spec development efforts started early in 2004, were refined by January 2006 and installation was completed by Skanska-Tully JV in June 2010. | 12 Ø Sodium Hypochlorite Tank Under 5.5 PSIG Shop Hydro Test |
Delaware's Justin Tanks Delivers FRPI Certified Tanks to Concord, MA WWTF The Concord Waste Water Treatment Facility in Concord, MA was the recent recipient of two Alum and two Caustic tanks, both requiring FRPI laminating process and laminate certification. CDM was the designer of this state of the art plant upgrade, which Justin Tanks LLC, Georgetown, DE was the tank manufacturer. With such stringent regulatory requirements, FRPI was chosen as the fiberglass tank quality verification program for this highly acclaimed facility. According to the town of Concord and Waterline Industries, the on-site contractor, the luminary treatment process involving a magnetically enhanced coagulation (CoMag) system will be showcased as the first of its kind. This facility is already gaining significant attention from communities within Massachusetts and as far away as China. Installation of the FRPI vessels three stories below ground level were completed as required.
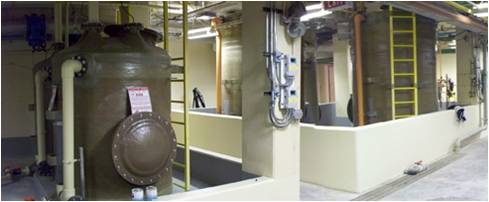 5 Ø Caustic and 8 Ø Alum FRP Tanks
|
|
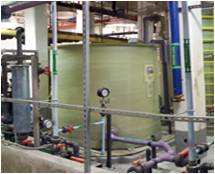 6 Ø Thickening Polymer Mixing and Aging FRP Tank
| Camp Dresser & McKee Specifes FRPI Certified Polymer Tanks in Brockton, MA Brockton Wastewater Treatment Facility Phase 2 Upgrade is the home of eleven (11) FRPI certified tanks ranging from 1,300 gallon Polymer tanks to 15,000 gallon Ferric Chloride tanks. Walsh Construction installed the vessels in Brockton, MA, which were specified by Camp Dresser & McKee, Inc. All of the vessels required FRPI laminating process and laminate certification and were fabricated and supplied by Justin Tanks LLC, Georgetown, DE. Final installation certification took place in March 2008. |
Town of Mansfield, MA Installs Ventilation System This FRPI Certified ventilation system installed by Methuen/TMD Construction is designed to handle 2500 fpm hydrogen sulfide and other odorous compounds at a design vacuum of 10 water column. The outdoor portion of the duct has a design differential temperature of 135 degrees F, which equates to a thermal growth of approximately 0.62 from the 30 Ø drop to the 90 degree elbow turning into the farthest Biofilter. Proper support design by the duct manufacturer, An-Cor Industrial Plastics, takes into consideration thermal expansion and contraction of both the horizontal and vertical sections of 30 Ø ductwork and results in stress free operation with expansion joints properly designed and located.
| 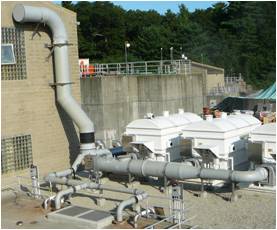 8 to 30 Ø FRP Ductwork on a Biofilter System inlet. |
|
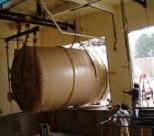 10 Ø FRP Sodium Hypochlorite Tank | First FRPI Certified Tanks Installed at Upper Blackstone Camp, Dresser and McKee specified FRPI Laminating Process and Laminate Certification for three (3) 10 15% Sodium Hypochlorite and two (2) 9 38% Sodium Bisulfite FRP chemical feed tanks needed by their client, the Upper Blackstone WPAD in Millbury, MA. Walsh Construction handled the purchase of the tanks from An-Cor Industrial Plastics and installation. The CDM lead project engineer commented that this was the first time she didnt have to worry about the quality conformance for the FRP tank section on one of her projects. Everyone on the project team volunteered how very pleased they were with the success of the installation and FRPIs Certification process! |
|
SESD Controls Corrosion with FRPI Certified Ductwork At the direction of the South Essex Sewerage District Project Manager in Salem, MA, Tighe and Bond Specified FRPI Laminate Certification for over 1,300 of large diameter round and rectangular ductwork needed to replace a failing stainless steel odor control duct system that was in service for less than ten (10) years. Enterprise Equipment Company, a subcontractor to Methuen Construction, purchased the ductwork, duct system engineering and installation support from An-Cor Industrial Plastics. The Owner, Engineer and Contractors said this is the smoothest installation and best looking ductwork they have seen. | 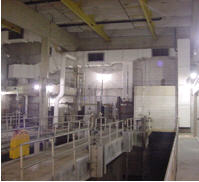 Rectangular & Round FRP SO2 Ductwork |
|
|
| |